PLC ≡ RIGHT: the right people, platforms, and outcome for any project.
The PLC RIGHT Process
Click thumbnail to download PDF. Evaluate Your Current System On-Site
- Develop And Agree On High-Level Plan
- Kickoff The Project
- Begin Hardware Design And Software Functional Description/Design
- Finalize: Hardware Design, Software Configuration, Develop Simulations And Internally Test Configuration
- Perform Customer Factory Acceptance Testing
- Install And Commission Hardware And Software
- Provide Post-Project Support
Keep reading for a deep dive into the details of all eight steps of PLC RIGHT.
Here's How It Works
STEP 1: Evaluate Your Current System On-site
During the PLC RIGHT evaluation stage, LSI listens to your vision for the new PLC and then performs an audit of your existing system in which we:
- Visit your plant and evaluate the current system.
- Evaluate and assess what new drawings, documentation and design considerations will be required.
- Identify and understand your business risks.
- Review current PLC program(s) to evaluate the quality of the PLC logic comments and code construction.
- Make recommendations based on the evaluation of the current PLC logic. Should it be converted or can it be re-programmed to take advantage of modern PLC functionality?
- If re-programming is chosen, we will prepare to implement programming standards prior to code development.
- Perform a PLC hardware upgrade analysis and provide recommendations.
- Gather information to determine how field wiring will be migrated.
- Many options exist here, including re-using the existing PLC I/O card swing arms to adapt to the new PLC card or a complete re-wiring. These decisions will directly impact production downtime, making proper planning essential in minimizing the impact on production.
- Determine ways to maximize operations and reliability.
- Identify opportunities to incorporate new technology and optimize the system.
STEP 2: Develop And Agree On High-Level Plan
Utilizing the information we learned in Step 1, LSI produces documentation that provides a high-level implementation plan to execute the PLC migration – the right way. This approach allows us to address the technology to be used (along with possible alternatives), as well as the constructability of the system, timeline and budget. Because we are an independent systems integrator, LSI focuses on what is best for your bottom line, not our own.
STEP 3: Kickoff The Project
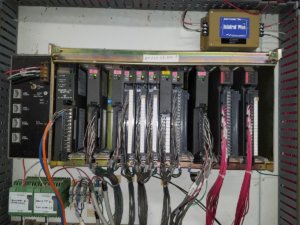
PLC RIGHT creates the necessary drawings of your legacy equipment to ensure that all plant details are accurate and up-to-date. This also fills in any gaps identified during the system evaluation phase. For larger projects, we spend time with your operations crew (maintenance technicians, plant operators, etc.) to document your process, learn about any unique issues and take note of the functional requirements of the system.
STEP 4: Begin Hardware Design And Software Functional Description/Design
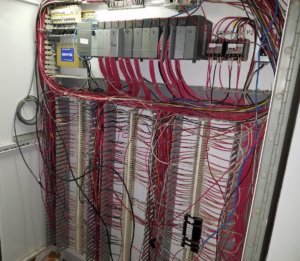
LSI’s team of experts goes to work producing plans for the new system. This includes hardware drawings and functional specification documents (if required) for the necessary software, all based on our evaluation in Step 1 (using agreed-upon standards). As we develop the design, we check in with you regularly to discuss your options, clarify requirements and gain your input throughout the process.
STEP 5: Finalize: Hardware Design, Software Configuration, Develop Simulations And Internally Test Configuration
During this step, LSI builds the control panels (or facilitates their construction), configures the software, develops right-sized process simulations and tests the new PLC configuration. We complete intermediate configuration reviews with you along the way to ensure that the Factory Acceptance Test is a success.
STEP 6: Perform Customer Factory Acceptance Testing
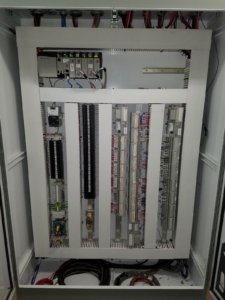
Taking place at our large training site (or your own location, if you prefer), we perform full simulations of the system for your approval. Validation is a major component of PLC RIGHT. Engineers who have been involved with the project are present for discussion, and changes can be incorporated in real-time.
We can then travel to your plant to perform on-site training with operators and maintenance teams using our simulation system. This step ensures that everyone involved is comfortable with the new system and understands it inside and out – before it is installed. This allows for a smooth transition between project development, execution, and long-term operation and maintenance of your facility.
STEP 7: Install And Commission Hardware And Software
PLC Panel after upgrade Once the system has been fully tested, LSI executes our plan, replacing the old hardware (as designed) and implementing the new software.
- Whether you have your own installation team or would like us to handle the contracting, we will work hand in hand with the electricians involved to perform the install.
- After the new PLC system is installed, we test 100% of the devices included in the new control system, ensuring operational success and system reliability.
- Any remaining legacy networks are tested as well, along with connections to other systems. (It’s the PLC RIGHT way to do things).
- LSI is on-site with you to run the entire process, with or without product, providing support and guidance.
STEP 8: Provide Post-Project Support
Following the project, LSI provides 24/7 support until all success criteria are fully met. We can also provide ongoing on-site or remote support per your request. Lastly, LSI provides As-Built system documentation to ensure that your new system is fully documented (as it has been installed) for you to have long-term support and maintenance.