The Situation
Every year, we have multiple variable frequency drive (VFD) failures on our rotating germination decks in our malthouse. Can LSI investigate the root cause and recommend a solution?
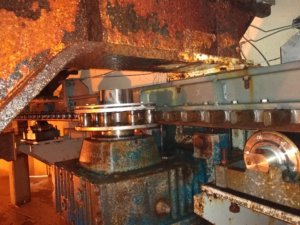
The largest single-site malting facility in the United States experienced VFD failures on all six rotating germination decks. For a 24/7 full-time operation, this unplanned downtime was causing lost production and driving up maintenance costs.
When the germination decks were installed in 1983, mechanical equipment alignment and tolerances were at their best for that era and the design used first-generation VFD drive technology. Each germination deck is mechanically coupled to a rack and pinion system consisting of five motor gearboxes that are physically located in a star configuration (see diagram) with the speed controlled by five VFDs.

The random failures first began occurring ten years ago and have now increased to eight failures a year. Each time a failure occurs, maintenance must balance the deck system by tweaking the PLC configuration for each VFD. Unfortunately, this is only a temporary fix until any new imbalance appears in the system.
The client turned to LSI for help with an increasingly unacceptable situation.
The Solution
LSI started by listening to the malting maintenance department to get a comprehensive history of mechanical and electrical changes over the years that would have exacerbated the issue. Next, we reviewed the deck speed control and the load sharing control scheme.
It became apparent that the mechanical wear and decades of electrical motor changes left the germination decks incompatible with the speed control scheme and were causing the legacy VFDs to fail at an alarming frequency. The system’s inability to adequately torque share and handle uneven mechanical loads caused by varying gearbox and deck bearing loads was the culprit. A new speed control scheme with improved torque sharing capabilities was required.
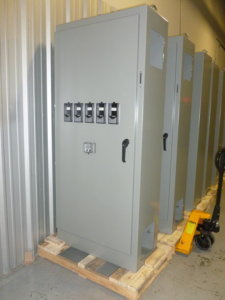
LSI recommended a “Droop Follower” for this application, which is a speed-controlled control scheme with robust load-sharing characteristics. This control scheme is one of the simplest methods of speed-controlled load sharing that matched the malting facility’s high uptime requirements. If any one of the five deck drives fail, the others take over and continue rotating the deck to keep production running. In addition, the Toshiba G2, G3, and G7 legacy VFDs were replaced with Rockwell Automation AB Powerflex 755 VFDs with adjustable droop capabilities.
LSI Provided
VFD Commissioning Professional services necessary for the mechanical and electrical design
- General Arrangement drawings, electrical drawings, controls drawings, and bid specifications for:
- Removal of existing equipment and installation of new VFD panels for each deck
- Integration of VFDs with “Droop” control using Sensorless Vector speed control and static motor tuning
- PLC configuration and VFD set-up and commissioning
- Construction technical oversight and sequencing to ensure that each deck system was installed in a compressed 3-day outage (to reduce downtime)
- Complete design and fabrication of the new VFD panels
The Results
Eliminated downtime
- Since the installation in May 2020 — zero downtime due to VFD failures!
Optimization
- Optimum speed control with robust load sharing was achieved.
- PLC load balancing logic was removed for better maintainability.
Standardization
- Standardized on a 480V VFD system instead of a one-off 230V system.
Minimal changes
- No germination deck electrical or mechanical adjustments were required.
- Existing motors and main power feeds were retained.
LSI Listens
LSI listened, then our team went to work developing and implementing a solution that eliminated the downtime-causing VFD failures and optimized the system for better performance.
Let LSI’s brewing team listen to your challenges.