Our Outdated Drives Are Putting Many Aspects Of Our Textile Manufacturing Process In Jeopardy, Including Our Crucial High-Speed Winders. Can Your Team Upgrade Our System And All Related Hardware Simultaneously?
What Our Client Said
The high-speed winders used in our textile manufacturing process are currently run by a discontinued Siemens MASTERDRIVE system. We are becoming more and more concerned that finding replacement parts for this outdated system will become impossible, resulting in unwanted downtime. Since our manufacturing process also utilizes additional legacy equipment that’s subject to fail in the near future, we need LSI to design a new equipment bay that would allow a simultaneous update to the drives, related legacy hardware and software code.
What We Heard
The chances of finding replacement parts for our outdated drives is becoming bleaker by the day. Due to the large number of machines we have that depend on these legacy units, it will become difficult to maintain operations as they begin to fail. We need LSI’s team of experts to help our facility get a head start on the situation by upgrading our drives along with other related legacy hardware and software code.
What We Did
Improved maintenance and reliability • Increased network speed • All items upgraded, installed and running in one week
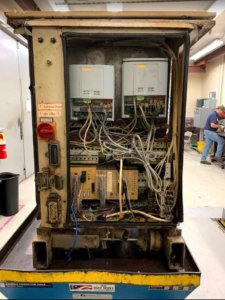
LSI’s team began by determining which combination of modern components would best replace the existing legacy hardware and controls. Because of its similarity and enhanced power capabilities, LSI engineers decided that a Sinamics S120 drive system would be the best option for replacing the existing Siemens MASTERDRIVES. LSI also upgraded the current S7-300 PLC with a new and improved S7-1500 PLC.
Next, the customer sent LSI’s team a spare high-speed winder and test control cabinet so the team could develop the new equipment bay and convert the previous Step 7 code to the latest TIA Portal Software (as well as retrofit the winder hardware for on-site testing). Each winder line consisted of either 8 or 12 positions. For each position, LSI’s team built a new back panel that included an ET200SP for the I/O coming from the field, as well as a main cabinet located in a cooling room that would contain the drives, PLC and other 480VAC hardware. LSI replaced the existing ProfiBus Serial Communications with the faster and more reliable ProfiNet Industrial Ethernet, which allowed hard-coded signals to be sent from the cooling room cabinets to each winder position via quick disconnect cable. In the end, LSI had everything installed and running within one week’s time.
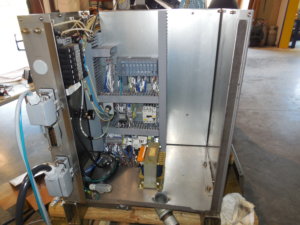
LSI provided:
- Engineering and design
- Systems integration
- PLC hardware
- Startup and commissioning
- Testing of completed system
- Retrofitting and upgrade of legacy equipment
The Results Speak For Themselves
Increased system reliability and productivity
By upgrading all the drives, related legacy equipment and software code at one time, LSI helped the customer dramatically decrease the chances of experiencing unplanned downtime due to potential legacy component failures. The upgrades increased confidence pertaining to maintenance, availability of replacement parts, and technical support on equipment for the future.
Improved network speed and flexibility
LSI’s decision to upgrade the ProfiBus serial interface to ProfiNet Industrial Ethernet immediately resulted in a faster, more reliable network, as well as improved communications to all equipment components. It also provided the customer with the ability to send hard-coded signals from each of the 12 winder positions.
Installation in one week, thanks to off-site preparation
By receiving a spare high-speed winder and test control cabinet from the customer, LSI was able to prepare the retrofit components for all winders and related hardware, as well as to perform all legacy component upgrades off-site. Not only did this allow LSI to research and design the updated system in a quick and efficient manner, it allowed the customer’s manufacturing process to continue with very little downtime. When it came time for final installation, everything was installed, retrofitted and running within one week.
LSI Listened
LSI listened, then we put our knowledge and experience to work, utilizing the best combination of technologies to simultaneously upgrade the customer’s outdated drives, related legacy hardware components and software code. In the end, network capabilities were faster and more reliable, and the risk of unplanned downtime was virtually eliminated.
Legacy systems can put a facility’s entire manufacturing process in jeopardy. By contacting LSI’s experts to upgrade its discontinued drives, related legacy hardware and software code simultaneously, this company was able to eliminate the risk of catastrophic downtime with very little disruption to its ongoing productivity.